Example: Pump Operating Point¶
A pump with the characteristic curve shown in the accompanying graph is to be installed as shown.
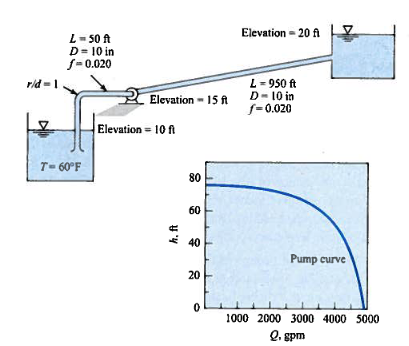
Caption¶
Determine the anticipated discharge in the system?
Step 1¶
State the problem, done above! But seriously we need to create a system curve \(h_p(Q)\) and superimpose it onto the pump characteristic curve shown to find the operating point.
Step 2¶
The sketch is pretty much done for us; so not much to add here.
Step 3¶
Knowns:
Pool elevations
Working fluid (water)
Pipe lengths and diameters, and friction factors (unusual to know these, but we could determine from material properties if needed)
Pump “location”
Fitting types
Unknowns:
\(h_p(Q)\)
\(Q\)
Step 4¶
Governing equations:
Modified bernoulli: \(\frac{p_1}{\gamma}+z_1+\frac{V_1^2}{2g}+h_p(Q) = \frac{p_2}{\gamma}+z_2+\frac{V_2^2}{2g}+\frac{fL}{D}\frac{V^2}{2g}+K_{entrance}\frac{V^2}{2g}+K_{bend}\frac{V^2}{2g}+K_{exit}\frac{V^2}{2g}\)
Darcy-Weisass pipeline loss model: \(h_{pipe loss} = \frac{fL}{D}\frac{V^2}{2g}\)
Continunity: \(Q=VA\)
Step 5¶
Analysis
Using modified bernoulli, observe constant diameter pipes and start and end at each reservoir pool surface so that
and
Rearrange what remains into
We will also need to employ continunity to relate \(Q\) and \(V\) as
def velocity(flow,diameter):
import math
velocity = (flow)/(0.25*math.pi*diameter**2)
return(velocity)
def system_curve(z1,z2,flow,plength,pdiameter,pfriction_factor,k1,k2,k3,gravity):
lift = (z2-z1)
velocity_head = (velocity(flow,pdiameter)**2)/(2 * gravity)
pipe_loss = (pfriction_factor*plength/pdiameter)*velocity_head
fitting_loss = (k1+k2+k3)*velocity_head
system_curve = lift+pipe_loss+fitting_loss
return(system_curve)
def gpm2cfs(flowgpm):
gpm2cfs = flowgpm/(7.48*60) # 1 cfs = 7.48gal/cf * 60 sec/min
return(gpm2cfs)
Now use these scripts to make a table of system curve values
flowgpm = [i for i in range(0,3750,250)] # list of flowrates
flowcfs = [0 for i in range (len(flowgpm))] # empty list for conversion
# convert to cfs
for i in range(len(flowgpm)):
flowcfs[i]=gpm2cfs(flowgpm[i])
addedheads = []
for i in range(len(flowgpm)):
addedheads.append(system_curve(10,20,flowcfs[i],1000,10./12.,0.020,0.03,0.35,1.0,32.2))
print("--- System Curve Table --- \n Flow (gpm) Added Head (ft)")
for i in range(len(flowgpm)):
print(" ",round(flowgpm[i],1)," ",round(addedheads[i],1))
--- System Curve Table ---
Flow (gpm) Added Head (ft)
0 10.0
250 10.4
500 11.6
750 13.7
1000 16.6
1250 20.3
1500 24.8
1750 30.1
2000 36.3
2250 43.3
2500 51.1
2750 59.7
3000 69.2
3250 79.5
3500 90.6
Now use this table to find operating point from the pump performance curve (draw system curve on the pump curve).
pumpflow = [0,500,1000,1500,2000,2500,3000,3500,4000,4500,4900]
pumphead = [76,75,74,73,72,70,67,59,50,22,0]
import matplotlib.pyplot as plt
plt.figure(figsize=(10, 8))
plt.plot(pumpflow,pumphead,c="red")
plt.plot(flowgpm,addedheads, c="blue")
plt.legend(["Pump Curve","System Curve"])
plt.title("Operating Conditions for Example System")
plt.xlabel('Discharge (gpm)')
plt.ylabel('Head (ft)')
plt.grid(which='both')
plt.show()
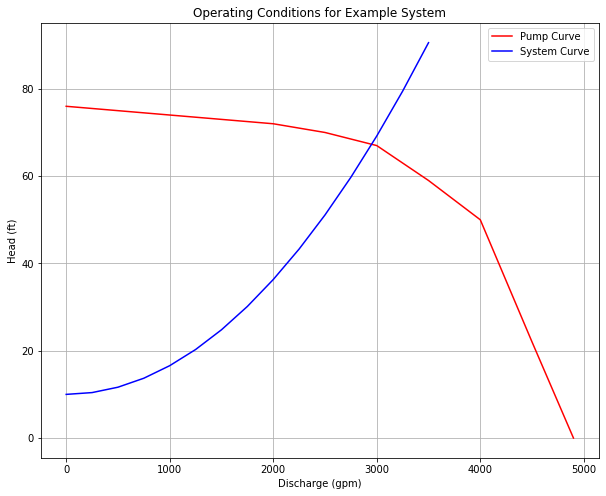
Step 6¶
We are done, and would report that the operating point is \(Q \approx~3000 \text{gpm } @ 70~\text{feet of head}\)
Readings¶
CE-3305-2022-1 Syllabus. http://54.243.252.9/ce-3305-webroot/0-Syllabus/ce-3305-2022-1-syllabus.html
Hibbeler, R.C, Fluid Mechanics, 2ed. Prentice Hall, 2018. ISBN: 9780134655413 pp. 569-596
DF Elger, BC Williams, Crowe, CT and JA Roberson, Engineering Fluid Mechanics 10th edition, John Wiley & Sons, Inc., 2013. http://54.243.252.9/ce-3305-webroot/3-Readings/EFM-20.pdf
Cleveland, T. G. (2014) Fluid Mechanics Notes to Accompany CE 3305 at Jade-Holshule (TTU Study Abroad 2015-2019), Department of Civil, Environmental, and Construction Engineering, Whitacre College of Engineering. missing_link